Benefits of Chromate Conversion
First, a little background on how the chromate conversion process works. Hexavalent chromium is used in the immersion bath process where the coating is applied. However, because Hexavalent is considered toxic, we also have non-hexavalent chromates that comply with the Restriction of Hazardous Substances regulations.
Military-Grade Products
Chromate conversion is intended for aluminum that is not anodized because it is used to repair anodized coating on aluminum. Type I and II conversions are used to protect against corrosion on unpainted items. It also helps for the paint to stick when the item is painted in the future. The corrosion protection of chromate conversion is what attracts the military to this process.
At Midwest Metal Products one of the areas we serve is the military. Why do they find the chromate conversion process helpful? Sometimes only certain surfaces “need” to be painted, an example of this is a military tank. The inside of a military tank paint finish is not required, but the outside is required. Usually, a Class 1A coating is used for military-related projects.
For electrical and electronic applications, Class 3 coating is effective because the coating is a lot thinner.
Chromate Benefits
The benefits of chromate conversion go on and on as it is useful for many reasons. It can be a corrosion inhibitor, primer, decorative finish, or retain electrical conductivity.
Retaining electrical conductivity can depend on the coating thickness of the chromate. So if you are looking for electrical conductivity from the chromate conversion process, you want to ensure that the chromate is the proper thickness.
As a corrosion inhibitor, chromate is often applied to galvanized parts to make them stronger. Darker colors provide more corrosion protection.
The durability is another one of the benefits of chromate conversion. When first applied, the chromate conversion is soft and gelatinous but hardens as it ages. If you need the product to cure faster, the process can be sped up by curing the product gradually reaching a temperature of 70° C but not over because it can damage the coating.
Most businesses use chromate conversion because it stops corrosion and there are a few options to choose from. It is also a good choice because it eliminates the powdery areas, scratches, and breaks you may have with traditional powder coating.
If you have any questions contact Midwest Metal Products. We will happily answer any questions you have by phone as well.
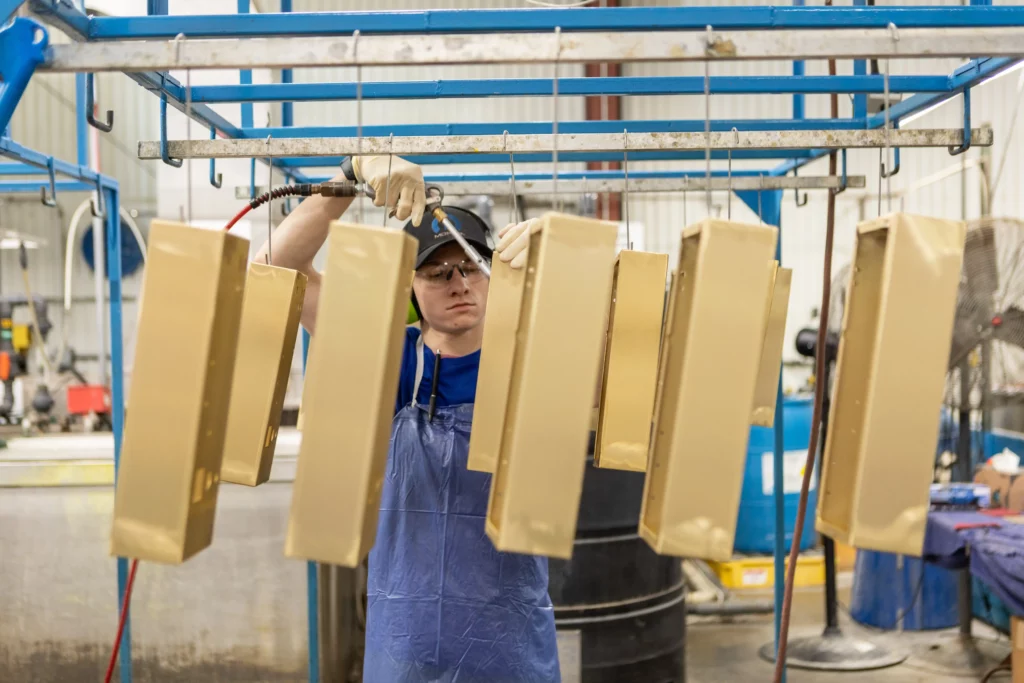