Welding Methods for Stainless Steel and Aluminum
Whether welding stainless steel or aluminum parts, a quality weld is always the goal. Besides having different qualities that can be beneficial for different industrial applications, these two materials weld differently, too. The biggest differences between the two welding methods are the cost of the materials and labor to weld them as well as their properties related to resistance to cracking, deforming, and corrosion.
Choosing aluminum or stainless steel often comes down to application. Steel products include structural building materials, agricultural equipment, heavy equipment, food industry equipment, and automotive products. Aluminum is more widespread in use for the aerospace, computer, and automotive industries. Both provide quality parts for their chosen application.
Welding the two materials differs considerably, a fact that our certified welders take into consideration. Stainless steel welding is fairly cost-effective, easier to learn, and more forgiving than aluminum welding. Aluminum welding involves more skill and cleanliness, but aluminum parts are lighter weight and resistant to corrosion. Stainless is 2.5 times heavier and much stronger than aluminum. It can bend and distort when welded but doesn’t crack as easily as aluminum. Keep reading to learn more about each type of welding and how we handle these metal part welding at Midwest Metal Products.
Aluminum Welding
In our welding department, we perform a lot of aluminum welding. Aluminum welding can be difficult to master due to its sensitivity to oxide and hydrocarbon contamination. The metal must be thoroughly cleaned, and the filler rod must also be completely free of contaminants. The workspace must also be kept pristinely clean to keep contaminants away from the aluminum welding materials. Our welders make sure to keep the weld shop very clean to reduce the risk of cross-contamination of different metals, substances, and particulates.
We employ two methods for welding aluminum: TIG welding and MIG welding. TIG welding uses a Tungsten Inert Gas welder, aluminum filler rod, and inert gases to achieve a weld for aluminum parts. It also works for other thin metals. MIG welding is an arc welding process that uses a Metal Inert Gas welding machine to feed metal welding wire through to a welding run. This fuses the two metals together. Again, inert gases further shield the metal weld from contamination.
Precise temperatures and techniques need to be used when welding aluminum. Our facility has been NADCAP Certified for aluminum welding since 2015. This requires our welders and facility to maintain high-quality standards for our welding work. Certification has also instilled more efficient operations throughout our part production facility.
Stainless Steel Welding
On the Midwest Metal Products production floor, we perform some stainless steel welding for the aerospace and food industries. One of the challenges of welding stainless steel is that the heat required for stainless steel welding can cause warping, discoloration, and a loss of corrosion resistance.
Another challenge with stainless welding includes warping. Fixtures to hold the parts must be very secure to ensure that warping does not occur. We work hard to ensure stable fixtures are in place for stainless steel welding. As for discoloration of stainless steel welds, we can use a technique that purges the part with an inert gas so the atmosphere doesn’t discolor the metal or cause weld contamination.
At Midwest Metal Products, our welding department specializes in sheet metal parts that are difficult to weld and are held to tight tolerances. Our skilled weld team takes every precaution to prevent problems with aluminum and stainless steel welds. We can repeatedly perform quality welds for durable and consistent joins, which we produce daily for our customers.
Learn more about our welding capabilities.
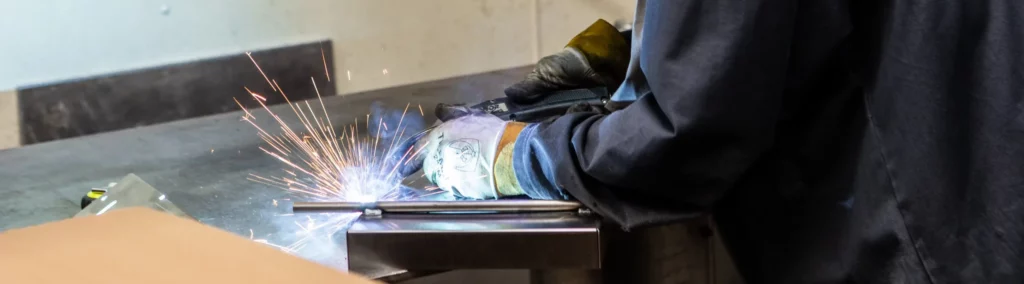